What is the melting point of polyester yarn
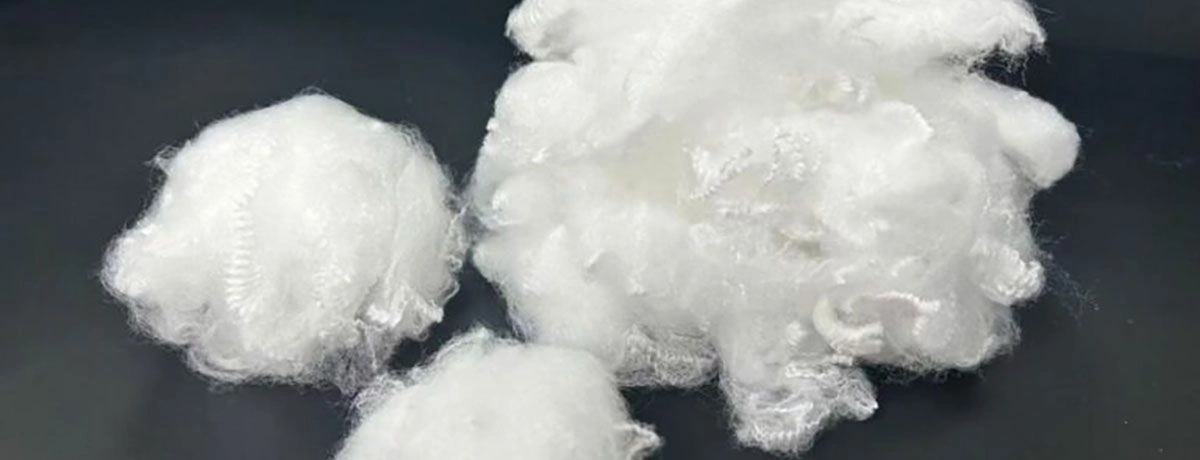
Introduction
When it comes to the garment industry, polyester yarn stands out as a staple material due to its versatility, durability, and cost-effectiveness. This synthetic fiber, known as polyester fiber, is ubiquitously found in everything from clothing to accessories, highlighting its extensive applications and ability to enhance the qualities of textiles. One of the most important properties to understand about polyester yarn is its melting point. Knowing the melting point can impact everything from manufacturing processes to garment care, ensuring quality and safety at every stage.
Understanding Melting Point
Definition and Importance in Material Science
In material science, the melting point is defined as the temperature at which a solid becomes a liquid under normal atmospheric pressure. This property is significant because it indicates how a material behaves under heat, specifically its thermal properties and processing behaviors. For synthetic fibers like polyester and rayon, the melting points determine their application in various industrial processes, from extrusion to dyeing.
Factors Influencing the Melting Point of Synthetic Fibers: Chemical Structure
Several factors influence the melting point of synthetic fibers. The chemical structure of the polymer, the degree of polymerization, and the presence of additives all play a role. Ethylene glycol is a crucial reactant in synthesizing linear polyesters like polyethylene terephthalate (PET), where it participates in ester interchange and direct esterification with terephthalic acid or dimethyl terephthalate. For polyester, these elements can alter its thermal stability and, consequently, its melting point. Understanding these factors helps manufacturers optimize their processes and improve the quality of the final product.
Melting Point of Polyethylene Terephthalate Yarn
Detailed Explanation of Polyester Yarn's Melting Point
Polyester yarn typically melts at a temperature range of 482°F to 500°F (250°C to 260°C). This high melting point and heat resistance are among the reasons polyester is favored in the garment industry. It allows for high-temperature processing, such as heat setting and dyeing, without degrading the fiber. However, exceeding this temperature range can cause the polyester to lose its structural integrity, leading to defects in the fabric.
How Different Manufacturing Processes Affect the Melting Point
The manufacturing process can also affect the melting point of polyester yarn. In non-equilibrium polyesterifications, acid chlorides are employed to achieve high molecular weights in the resulting polymers. For instance, the introduction of stabilizers and plasticizers during polymerization can enhance the thermal stability of the yarn. On the other hand, improper cooling rates during extrusion can lead to uneven crystallization, lowering the melting point. By controlling these variables, manufacturers can ensure that the polyester retains its desired properties throughout production.
Applications and Implications
Practical Uses of Knowing the Melting Point in Garment Production
Understanding the melting point of polyester is crucial for several practical applications in garment production. For example, in heat setting, where the polyester fabric is exposed to high temperatures to stabilize its dimensions, knowing the exact melting point ensures that the fabric does not warp or degrade. Similarly, in dyeing processes, maintaining temperatures below the melting point prevents the dye from bleeding or the fabric from weakening.
Heat Resistance and Safety Considerations for Garment Care and Manufacturing
Safety is another critical aspect influenced by the melting point of polyester. In garment manufacturing, maintaining environmental temperatures below the polyester’s melting point reduces the risk of accidental fires. Additionally, for end consumers, knowing the melting temperature helps in providing care instructions, such as avoiding high-heat settings in dryers, to preserve the integrity of the garment.
Case Studies
Case Study 1: Comparison of Two Garment Production Lines
In a detailed comparative study between two garment production lines, a significant difference was noted in their handling of polyester fabrics. The first production line was well-informed about the melting point of polyester yarn, a critical factor in fabric production, while the second line operated without this crucial knowledge. The informed line, with its understanding of the polyester yarn's melting point, exhibited remarkable fabric integrity and a significantly lower rate of defects in the final products. This knowledge empowered them to fine-tune their heat-setting processes, carefully controlling the temperature to avoid damaging the yarn while achieving optimal fabric properties. As a result, not only did they produce higher-quality garments, but they also significantly reduced waste. This reduction in waste not only had a positive impact on the environment but also improved the overall efficiency and cost-effectiveness of the production process. This study clearly illustrates the importance of technical knowledge in enhancing product quality and sustainability in garment manufacturing.
Case Study 2: Garment Accessories Shops
A number of garment accessory shops have reported significant improvements in product quality through a deeper understanding and application of the knowledge surrounding polyester yarn’s melting point. By meticulously selecting accessories made from polyester fibers capable of withstanding higher temperatures, these shops have successfully enhanced both the durability and overall appeal of their products. This strategic move has not only led to increased customer satisfaction but also fostered a higher rate of repeat business. The shops’ attention to such technical details has allowed them to stand out in a competitive market, demonstrating the value of integrating textile science into product selection and design.
Case Study 3: Temperature Control in Garment Factories
In garment factories, effective temperature control is paramount in preserving the quality of polyester yarn and other fibrous materials, which are key in the production of various textiles. Factories that have implemented rigorous temperature monitoring systems have witnessed a noteworthy decrease in product defects. By precisely regulating the environment, these factories ensure that the polyester yarn retains its structural integrity from the beginning to the end of the manufacturing process. This meticulous attention to temperature control not only mitigates the risk of defects but also leads to the production of more consistent and reliable products, ultimately enhancing customer satisfaction and trust in the brand. Such practices underscore the critical importance of environmental control in the textile industry and its direct impact on product quality.
Case Study 4: Implementing Safety Measures
Insights gathered from garment factories, which took proactive steps by implementing safety measures informed by the specific knowledge of polyester yarn's melting point, have revealed a significant reduction in the risk of fires. These factories maintained operational temperatures within safe limits, a critical factor given polyester's propensity to ignite at high temperatures. Additionally, by investing in comprehensive training programs for staff on the importance of effective thermal management, these establishments were able to mitigate potential hazards. This strategic approach not only ensured a safer working environment but also highlighted the importance of industry-specific knowledge in preventing workplace accidents. Through such measures, these factories have set a benchmark for safety in the garment manufacturing sector, demonstrating that informed and well-implemented safety protocols can lead to a marked decrease in workplace risks.
Conclusion
Understanding the melting point of polyester yarn is not just a technical detail—it is a critical factor that impacts the quality, safety, and efficiency of garment production. For garment accessories wholesalers, shop owners, and factory operators, this knowledge enables better decision-making, from selecting materials to optimizing manufacturing processes. By integrating this understanding into daily operations, businesses can enhance product quality, ensure safety, and ultimately gain a competitive edge in the market.
For those looking to explore further, consider connecting with industry experts or leveraging advanced tools to monitor and manage the thermal properties of your materials. Knowledge is power, and in the world of garment manufacturing, it can also be the key to success.